At Salazar Packaging, we specialize at developing custom packaging solutions that are competitively priced and as green as possible. They vary from a wide variety of packaging papers including indented, bogus, Kraft and even tissue to biodegradable air pillows and “bubble on demand” type solutions. We also offer an endless array of custom-fabricated corrugated products including inserts, corner protectors and shock-absorbing designs. Some are basic void fill, while others provide critical blocking and bracing to preserve and protect the contents being shipped.
Quite often, a customer contacts us requesting a quote for one or another based on their “self diagnosis” of the packaging challenge and ends up buying a product different from the one they originally asked for. This happens because all too often the self diagnosis is incorrect, not the BEST solution for their application or there is a better product that they did not even realize was available. In no area is this confusion more common than applications involving molded pulp trays and corrugated partitions.
Which Green Packaging Solution is Better?
That question is frequently asked of us, and potential customers are surprised to find out that they, rather than we, have the answer. It is only through an application review (usually at no cost or obligation) that we are able to make that determination, followed by a very confident product/solution recommendation. The factors we consider include:
- What is shipping, and how is it being shipped? A single case of glassware shipping FedEx requires a completely different solution than the same product being packed into cases and shipping on a pallet via LTL truck.
- What are we trying to protect it from? Is the concern stacking strength or “outside/in damage?” Perhaps the objective is to prevent products from damaging each other during shipment.
- What is the value of the products being shipped? We are sensitive to the fact that not every application can justify the cost of the “best” solution.
- What is the volume, and do you expect it to repeat? If so, how often? This is extremely important in regards to tooling. If it is a one-time-only shipment, we will try to steer you toward a product that does not require an expensive cutting die.
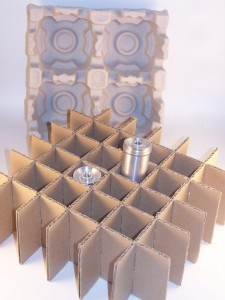
16-CELL PARTITION AND 4-CAVITY MOLDED PULP TRAY
The Purpose and Advantages of Partitions
Partitions are very versatile, relatively economical and available in small quantities. They can be ordered unassembled to conserve storage and shipping space, as well as pre-assembled to reduce packaging time and labor cost. Partitions are also considered very green packaging because they are usually made of paperboard or corrugated containing a high, though varying, percentage of recycled content. Plus, they are easily recyclable. There are no “stock or standard size” partitions, but they are made with no tooling, which makes custom sizing very affordable, even for small quantities.
In terms of application, they are usually used to separate products within a case to keep products from banging against each other in shipment or even to prevent label-to-label abrasion. Another very common purpose of partitions is to increase stacking strength, as most warehouses work to conserve space or prevent damage when pallets of products are stacked in shipment.
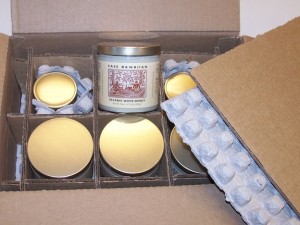
VOLCANO ISLAND HONEY PARTITIONS WITH PERIMETER AIR CELL
Shock-absorbing products such as our Eco Flex molded pulp can easily be added over and under a partition to improve drop/shock damage when cases are shipping individually. (See Volcano Island Honey photo at right). In that particular application, we also added a perimeter air cell to prevent outside/in damage. Air cells can also be used to help a custom-size partition “fit” into a stock size shipping box, minimizing inventory dollars, space and cost.
The Purpose and Advantages of Molded Pulp
Molded pulp trays or clamshells can also be used to separate products in shipment, but typically their primary purpose is to completely encapsulate and immobilize. Due to cost and the tooling required, they are usually used to protect higher value or more fragile products. Even though top and bottom trays can be designed and used for bulk (case) shipments, in most applications one or just a small count of products is being shipped together. Trays and clamshells can be designed to provide excellent drop-shock protection by providing an acceptable “crush zone” around the product’s perimeter. They can also be designed to fit within a stock box size minimizing cost and inventory.
Tooling remains the largest hurdle for molded pulp, but we offer low-cost tooling, making this a viable and affordable option even for relatively low-volume applications. There are also some stock molded pulp trays for popular applications with common dimensions such as candles or wine bottles, but custom is the way to go if your product is unusual in shape or size and a snug fit is important.
“I would rather work directly with the manufacturer”
Some manufacturers sell direct to end users, as well as through agents and distributors like us. In an effort to buy at the lowest possible cost, it is not at all unusual for end users to attempt to buy directly from the manufacturer and “eliminate the middleman.” Even though the strategy may appear to be a good one, it is not necessarily a wise or cost-saving move if you do not end up with the best or lowest cost solution for your application. Understandably, manufacturers tend to sell what they make and may not be willing or knowledgeable enough to suggest a different product that perhaps they do not offer.
Applications are rarely as simple as they may appear and seldom is there a good, “one size fits all” solution. In fact, oftentimes we have found the best solution is a combination of different products that may only be available from two or three different manufacturing sources. That is what makes our almost 50 years of experience and variety of green packaging solutions so valuable.
Please contact Salazar Packaging to discuss your specific needs, and we will help guide you to making an informed and cost effective decision.
Related posts:
Green Packaging Solutions: Seven Things You Probably Did Not Know about Corrugated Partitions
The Greenest Packaging Option Is Becoming the Easiest Packaging Option